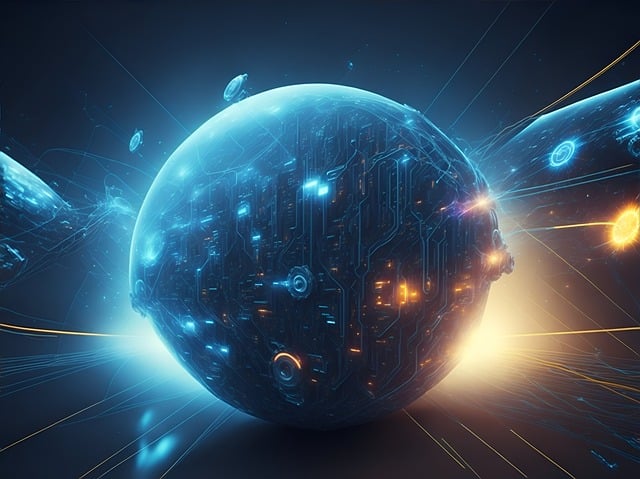
Introduction
In recent years, 3D printing has revolutionized industries, reshaping how products are designed, manufactured, and even consumed. This cutting-edge technology allows the creation of three-dimensional objects from a digital file by adding material layer by layer, a process known as “additive manufacturing.” Once confined to specialized fields like aerospace and medicine, 3D printing is now accessible to hobbyists, educators, and businesses of all sizes. Whether you’re curious about how 3D printing works, its practical applications, or how to get started, this guide will give you a comprehensive introduction to the exciting world of 3D printing.
What is 3D Printing?
3D printing is a method of creating physical objects from a digital design by laying down successive layers of material. Unlike traditional manufacturing techniques such as subtractive manufacturing (where material is removed from a solid block to shape an object), 3D printing is additive, meaning material is gradually added to form the desired object.
The process begins with a digital model, usually created in 3D design software such as CAD (Computer-Aided Design). This digital blueprint is then sent to a 3D printer, which interprets the file and builds the object layer by layer, usually using materials like plastic, resin, or metal.
How Does 3D Printing Work?
To understand 3D printing, it’s essential to break down the process into simple steps:
1. Creating a Digital Model
The first step in 3D printing is creating a digital model of the object you want to print. This can be done using various 3D design software tools such as Tinkercad, Fusion 360, or Blender. These programs allow users to design anything from simple shapes to complex, intricate structures. If you are not skilled in 3D design, there are plenty of online repositories like Thingiverse or MyMiniFactory where you can download pre-made designs for free.
2. Slicing the Model
Once the digital model is ready, it needs to be “sliced” before printing. Slicing is the process of dividing the digital model into thin horizontal layers. Each layer is translated into instructions for the 3D printer, telling it how to build the object step by step. This task is performed using slicing software such as Cura or PrusaSlicer. The output file is usually in G-code format, which the printer uses to guide the printing process.
3. Printing the Object
With the sliced file ready, it is transferred to the 3D printer via a USB drive, SD card, or wireless connection. The printer follows the instructions in the G-code file, depositing material layer by layer to create the object. Depending on the size and complexity of the object, printing can take anywhere from a few minutes to several hours or even days.
4. Post-Processing
After printing, the object may require some post-processing. This might include removing support structures (used to hold parts of the object in place during printing), sanding rough edges, or applying additional finishes like painting or polishing. Some materials, such as resin, require curing under UV light to harden fully.
Types of 3D Printing Technologies
There are several types of 3D printing technologies, each with its advantages and disadvantages. The most common methods include:
1. Fused Deposition Modeling (FDM)
FDM is the most widely used 3D printing technique, especially for hobbyists and beginners. It works by melting plastic filament and extruding it through a nozzle to build the object layer by layer. FDM printers are relatively affordable and can print a wide range of materials, including PLA, ABS, and PETG.
2. Stereolithography (SLA)
SLA uses a liquid resin that is cured by a UV laser to create objects. This method allows for higher precision and finer details compared to FDM, making it popular for applications like jewelry making or dental work. However, SLA printers are typically more expensive, and the post-processing (curing and cleaning the resin) is more involved.
3. Selective Laser Sintering (SLS)
SLS uses a laser to sinter (fuse) powdered material, usually nylon or other polymers. This technique produces strong, durable parts with complex geometries. SLS is often used for industrial applications, particularly in automotive and aerospace industries. However, it is less common for consumer use due to its high cost and complexity.
4. Digital Light Processing (DLP)
DLP is similar to SLA in that it uses light to cure resin, but instead of a laser, it uses a digital projector screen to flash a single image of each layer at once. This can result in faster print times compared to SLA while still maintaining excellent resolution and detail.
Applications of 3D Printing
The applications of 3D printing are vast and continue to expand as the technology evolves. Here are some notable industries where 3D printing has made significant impacts:
1. Healthcare
One of the most revolutionary applications of 3D printing is in the healthcare industry. Surgeons can create patient-specific models of organs or body parts to plan surgeries, and prosthetics can be custom-made to fit individual patients. Researchers are even exploring bioprinting, where 3D printers use living cells to create tissue or organs.
2. Aerospace and Automotive
Aerospace and automotive industries benefit from the lightweight, durable parts that 3D printing can produce. Aircraft manufacturers like Boeing and Airbus use 3D printing to create parts that are lighter and more fuel-efficient. The ability to create custom components also streamlines the production process, reducing waste and costs.
3. Education
3D printing is increasingly used as a teaching tool in schools and universities. It allows students to bring their designs to life, promoting creativity and problem-solving. It also serves as a hands-on learning tool in fields like engineering, architecture, and art.
4. Consumer Products
The customization potential of 3D printing has opened new doors for the consumer product industry. Companies are now offering custom-made products, from eyewear to shoes. Small businesses and entrepreneurs use 3D printing to create prototypes and end products without the need for expensive tooling and molds.
How to Get Started with 3D Printing
If you’re new to 3D printing and want to explore this exciting technology, here’s how to get started:
1. Choose the Right 3D Printer
The first step is to choose a 3D printer that suits your needs and budget. For beginners, FDM printers are often the best choice due to their affordability and ease of use. Popular models include the Creality Ender 3 and the Prusa i3 MK3. If you’re interested in printing more detailed objects, consider an SLA printer like the Anycubic Photon.
2. Select Your Materials
The most common materials for beginners are PLA and ABS filaments. PLA is biodegradable and easy to work with, making it ideal for hobbyists and home users. ABS is more durable but requires higher temperatures and better ventilation. As you gain experience, you can explore other materials like PETG, nylon, or flexible filaments.
3. Learn 3D Design
While you can download pre-made designs, learning to create your own models opens up endless possibilities. Start with beginner-friendly software like Tinkercad, which offers a simple interface for basic designs. As you advance, you can move on to more powerful tools like Fusion 360 or Blender.
4. Experiment and Practice
Like any new skill, mastering 3D printing takes time and experimentation. Start with small, simple projects to familiarize yourself with your printer and software. Learn from online communities, forums, and tutorials to improve your technique and troubleshoot common issues.